(1)トラッピング不良
多色機を用いて多色印刷を行う際、先に印刷したインキの上に次のインキが転移することをトラッピングという。もともと、トラップ(trap)とは「罠で獲物を捕獲する」という意味で、印刷においては多色刷りの場合、先に刷ったインキ層が後に刷るインキをうまく捕らえる現象をいう。すなわち「印刷されたインキ被膜が、次のインキ被膜を適当に受理する能力」と定義づけられている。トラッピングは、多色印刷でインキを転写していく場合、必ず起こる正常な現象であるが、うまくいかないと色むらとなり、トラブルとなる。先刷りのインキが後刷りインキを受け付けないで、後刷りインキが綺麗に転移しない現象をトラッピング(インキ転移)不良という。
ウェット印刷で各色を適正にトラッピングさせるには、用紙上の、まだ濡れている状態のインキが後刷りのブランケットからインキを剥がし取るだけのタックを持っていることが必要である。すなわち、先刷りインキのタックが後刷りインキのタックよりも高いことが重要で、逆に先刷りインキのタックが後刷りインキよりも低いと、すなわち先に印刷したインキの粘性よりも、後印刷の粘性が大きいと、後のインキは自層内で分裂できないで、先刷りインキの層内で分裂が起こりインキが取られてしまう。つまり、紙上の先刷りインキが後刷りのインキに取られ、後のインキが転写されないことになる。
トラッピングは、先刷りインキが後刷りインキを捕獲する正常な現象であるが、逆に、紙面に正常に印刷された先刷りインキが後刷りブランケット胴に不規則に取られる現象を「バック(逆)トラッピング(backtrapping)」という。この現象によって、先刷りインキが紙面から後のブランケット上のインキに不規則に取られ混じりあって、後刷りインキの色調が濁るとともに、印刷物は印刷むら(着肉むら)として目視されトラブルとなる。なお、バックトラッピングを広義にトラッピング不良の意に用いることもある。
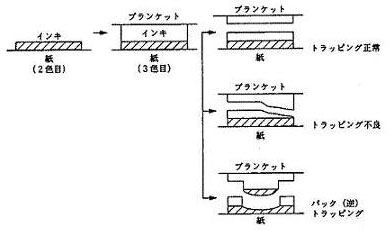
ここで、右図にモデルとしてトラッピング発生原理図を示すが、逆トラッピング現象は4色以上の多色印刷で起こりやすく、印刷胴数が多くなればなるほど、すなわちトラッピング回数が多いほど、その程度は悪化する。また、通常の湿し水を使用する印刷でも、使用しない水なし平版印刷でも発生する。この点、湿し水に関係する、後述の水負けトラブルとは異なる。なお、4色以上の印刷で着肉むら発生の場合に、最終胴を開放してみてむらが軽減されれば逆トラの可能性が大きいといえる。
4色印刷の場合、普通、刷り順は墨・藍・赤・黄であるが、この「逆トラ」現象は、2胴目の藍で、かつその面積が多く、3胴目の赤との重色(例えば、青空などの絵柄)になったときにシャドー部からベタ部にかけ発生しやすく、目立ちやすい。このため特に本トラブルを「藍むら」と呼ぶことがある。
コピーのため判りにくいが、参考までに着肉むら(藍むら)印刷物の写真(青空部の一部)を次に示す[左…良品、右…着肉むら(藍むら)品…プリンターによる複写]。
着肉むら(藍むら)写真
[左…良品、右…着肉むら(藍むら)品]
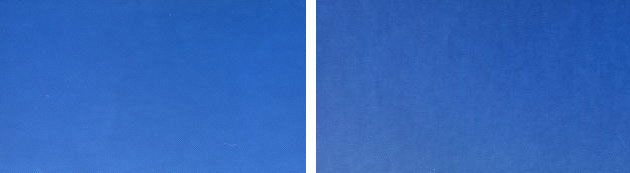
なお、その措置として、藍と赤の刷り順を変え、2胴目を赤、3胴目を藍にすることによってこのトラブルを軽減ないし解消できることがある。ただ、この場合、色合いが変わる恐れがあるので、その時は製版等での対応が必要になる。さらに、ウェットトラッピング (注1)は、何分の1秒という短時間に行われるから、先刷りにセット(あるいは乾燥性)の速いインキを使用することも、後刷りインキとのトラッピング性がよくなるので効果がある。また、後刷りインキのタックを下げることにより軽減することもある。
従って、多色機における各色間のウェットトラッピングを正常に行うために、各間のインキにタック差を持たせる必要がある。なお、ここでいうタックとは、インコメーターで測定されたインキそのもののタックでなく、印刷実機上あるいは紙上でのタックであり、差をつけている。すなわち、一般的に1胴目に使用されるインキタックが最大で、後胴に行くほど低くなっており、そのようなインキが使われている。
先刷りインキは、印刷されればすぐに、印圧によって表面粘度が上昇し(アフタータック)、次のインキをとらえやすくなるので、インキのタックが同じでもトラッピングは正常に行われる可能性がある。しかし、前述のようにトラッピングをよくするために、通常は先刷りインキタックを後刷りインキより高くするというタックバランス(タックグレード)をとる必要がある。つまり刷り順でインキタックを変化させることにより、刷り重ねがうまくいく。しかし、用紙や他の印刷媒体の種類、特性、印刷速度、温度、インキ量、画線部の面積、インキの湿し水特性などによって変わることがあるので、注意も必要である。
例えば、吸油性の少ない紙、浸透の遅いインキを使用した場合や、2~3色の先刷りにベタ面がある場合には、その後から印刷されるインキとの粘度差が少なくなり、トラッピング性が悪くなる。このときは、「藍むら」とその措置のところで述べたように、刷り順や使用するインキのセット性・タックなどを考慮する必要がある。また、フィルムや金属板・箔などへの印刷は、インキの浸透がないことから、下刷りインキの粘度上昇が少ないためにトラッピングしにくい。このため刷り順ごとにタック差(先刷りインキほどタック値を高く設定)を通常の紙の場合よりもさらに大きく取ることが必要である。
トラッピング不良によるむら対策としては、上記の印刷上の対応・措置以外に他紙で印刷をしてみて、印刷か用紙か判定し、印刷条件の修正や用紙の入替えが行われることが多い。用紙サイドでは、塗工時の乾燥パターンの適正化、塗料組成の修正(特にラテックスの選定)や、特にユニットタイプの4色以上の多色オフセット印刷機ないしRIテスターでの印刷試験評価による、製品出荷などの対応が行われている。
(2)クリスタリゼーション
クリスタリゼーション(crystallization,結晶化の意)とは、先刷りしたインキがガラス面のような乾燥状態になり、後に刷るインキが乗りにくくなる現象のことをいう。後刷りインキが先刷りインキにはじかれて均一に乗らないか、いったん付着したように見えても、擦ると容易に剥離する状態をいう。
これは先刷りのインキ中に存在する成分が乾燥過程でインキ被膜表面に残り、後刷りインキのビヒクルの浸透を妨げることによって発生する。具体的には、インキ中の不乾性油やワックス分が下刷りインキ表面に浸み出してくることが主原因で、桐油の多いインキや、結晶性ワックスを配合したり、ドライヤーが多く乾燥性が強すぎるインキを使用した場合や、毛細管現象が小さく吸油性が低い傾向のある用紙で発生することがある。原因となる先刷りインキの乾燥を多少遅めに調整するとか、乾き過ぎないうちに次の印刷をするとか、おるいはインキメーカーに相談するのがよい。なお、クリスタリゼーションは、単色機での刷り重ねを刷る場合の先刷りインキが乾いた状態(いわゆるドライプリント)で後刷りのインキがうまく乗っていかない現象であり、多色印刷機での各インクを同時印刷した場合の先刷りと後刷りのインキの間にみられるウェットトラッピング不良現象とは異なる。
付記
用語説明
注1)ウェットプリンティング、ウェットトラッピングなど
多色印刷機で2色以上を連続的に印刷する際に、1色印刷した直後、まだそのインキが乾かないうちに、次の色を刷り重ねることをウェットプリンティング(ウェット印刷、wet priting,wet on wet priting)といい、濡れている状態の先刷りインキが後刷りのインキを受け付け、転移することをウェットトラッピング(wet trapping)という。
このウェットトラッピングに対して、ドライトラッピングは、単色機で印刷を繰り返す場合のように、先刷りインキが十分にセットし、乾燥がある程度進行している上に、次のインキを転移させることをいう。一般的には、ウェットトラッピングよりトラッピング性がよい。ただ、先刷りインキが乾きすぎていたり、ワックスコンパウンドや裏移り防止剤、ドライヤーなどを過度に加えたり、先刷り印刷でスプレーパウダーが多い場合には、ドライトラッピングは悪化することがある[(2)のクリスタリゼーションの項参照]。