グロスゴースト、ドライダウンなど
今回はグロスゴースト、ドライダウンなどについて触れる。
グロスゴースト
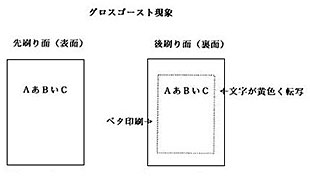
グロスゴーストはごくまれな現象であるが、印刷の段階では発生しなく印刷直後の発見が難しいこともあり、厄介なトラブルである。なお一般にいうゴースト現象は、ベタ刷り部分にインキの供給が間に合わないため、濃度のぼやけた部分が現れることをいい、これについては、すでに触れた「紙の基礎講座 印刷編(5) 縞・ミスチング・ゴースト・給・排紙不良」参照。
このゴーストに対して、グロスゴーストは、その名のように光沢差により影がでる現象で、下記のような状況で発生する。先刷り面(表面)に文字・絵柄を印刷し、棒積み後、反対面(裏面)にベタ刷りをしたように場合、数日後に見たらベタ面に先刷りと同じ文字・絵柄が現れていることがある。これがグロスゴーストである(右図参照)。
すなわち印刷し、パイルしたとき、上の紙の裏面白紙部に下の印刷物(先刷り印刷面)の絵柄どおりに光沢差による影ないし黄色い着色部が現れる現象をいう。この現象は一般的に印刷棒積み後、1日から1週間ぐらい経ってから現れるので対応面からも面倒なトラブルである。
これは先刷りインキ中のビヒクル分が浸透によって、裏面のその部分に当たった後刷りインキの浸透が押さえられて、光沢が上がり影が発生すること、および先刷りインキが乾燥する過程で発散する分解生成ガスが、紙面に吸着され、裏面のその部分に当たる後刷りインキの乾きを促進して、光沢を高め、他の部分と光沢差となって現れることが原因である。インキ被膜から発生するガスは、インキ乾燥時のビヒクルの酸化重合反応により発生するもので種々の成分を含んでいるが、ドライヤーのようにインキの乾きを促進する作用があり、ガスに触れていた印刷面は速く乾燥する。この結果、他の部分より光沢が高くなり、先刷りした同一模様の文字・絵柄がうっすらと影として出ることとなる。
このトラブルは、特に乾性油成分の多いグロスタイプのインキを使用し、ドライヤーの添加量が多く、かつインキ盛り量が大で、棒積み印刷物の高温での長期保管や、マット印刷および後刷りの絵柄が墨ベタ部などのときに発生、目立ちやすい。用紙では、密着性がよくてガスが抜けにくくなる、高平滑で光沢のあるアート紙などの高級塗工紙(アートポスト含む)に起こりやすい。しかし、用紙での対応策として塗料組成修正などをとれば紙質(風合)の変更を伴うことになり、実質的には対応は難しい状況にある。
そのため対策としては、後刷りまでの時間を長く(少なくとも1日以上)取ること、ベタの多い面を先刷りすること、乾性油量の少ない溶剤型インキ(クイックセットタイプ)でドライヤー添加量の少ないものを使用すること、かつインキ盛りを減らし、支障のない範囲でスプレーパウダーの散布量を増やすこと、棒積み枚数を減らすか、できるだけ少量の板(簀の子)取りをし、印刷後の風入れを励行すること、また印刷後のパイルは、高温多湿を避け、なるべく冷所に保管することや長時間の棒積みは避けることなどが効果がある。
季節的には空気が乾燥しており、静電気が発生しやすくて印刷物間が密着しやすくなる冬期に発生しやすいが、いずれにしても発生するガスを溜めないで抜く風入れが特に有効的である。またトラブルが発生した印刷物に、光沢差をなくすために、艶出し加工(OPニス、ビニール引きなど)やベタ部を再度印刷するなどの救済策が行われることもある。ただ、救済のためにトラブル発生面にマットニスを刷ると、逆に極端に目立ってくることがあるので、影にグロスがある場合には処置としては艶ニスを用いる。
なお、グロスゴーストはグロスゴースティング、ケミカルゴースト、グロスマイグレーション、オイルマイグレーションとか、ガス抜けと呼ぶことがある。
また、ただ単にマイグレーション(migration)ということもあるが、もともとマイグレーションとは「移行」という意味であり、印刷では印刷物を巻取りまたは積み重ねたときに、印刷面に接した印刷媒体(紙など)の背面部にインキ成分が移行して変色する現象をいう。変色は耐溶剤性の劣る着色料を用いた場合にその着色料が移行する、すなわち色料の昇華、溶融化などによる場合と、インキ中のビヒクル成分が反応して油が滲み込んだように黄色く着色、黄変させることをいい、グロスゴーストとは区別して使われるべきであるが、両方を合わせて「マイグレーション」として使われることがある。
ここで、印刷ではないが、ボールペンでの筆記による類似のトラブルを紹介する。あるユーザーが上質ノート用紙に外国製の油性ボールペン(黒)で記入し、半年ぐらい経過したところ対面紙の白紙部に筆記文字が黄色く転写しているとのことで、そのユーザーが苦情を申し入れたとして、ノート会社から調査を求められたことがある。
本件は印刷トラブルの一つである「マイグレーション」現象と同一であると考え、国内の主力ボールペンメーカー3社に問い合わせたところ、原因として紙の要因は無いか、あるいは有っても極めて小さく、インキ中の成分に起因するものであるとのことであった。それによるとトラブルを起こした油性ボールペンの油分が「オイルマイグレーション」を起こして黄色く転写したものか、他にインキ成分中の染料が「昇華(固体が直接、気体になること)」というマイグレーション現象を起こしたことも考えられるが、インキ成分が不明なので特定しにくいとの由。しかも、それを再現することはなかなか難しいとのことであった。なお、3社いずれともこれまでに同様な経験をしており、現在はインキ成分の修正により本件のようなトラブルは皆無とのことであった。
ドライダウン(dry down)
印刷直後には、艶(つや)があり冴えた色であった印刷物が、インキが乾燥していくと艶が薄れ色も浅くなることが多い。このように一般に印刷された直後のインキ濃度、光沢に対し、インキが乾燥するにつれて濃度、光沢が低下する現象をドライダウンという。なお、特にインキ濃度低下現象をドライダウン、インキ光沢の低下現象をドライバックといい、区別することがある。下図にはドライダウンの原理図(左)と紙質とドライダウン(例)…インキ被膜の形状変化(モデル)…を示す。
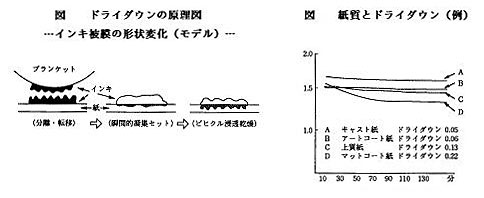
この現象の発生機構は、印刷時にインキが紙に転移した状態ではインキ被膜は平らにセットされている。その後、インキのビヒクルが紙に浸透し、乾燥した状態では被膜面は凹凸状になり、この面に光が当たると乱反射を起こし、光沢感が減じられ濃度が淡くなるものである。なお、インキ濃度計で色濃度を測ってみても、時間とともに濃度が薄くなっていくことが分かる。
また、紙質によってインキセットから乾燥して落着くまでの間の濃度に差がある。例えば、一般的にダル・マットコート紙はグロス系のアート・コート紙と比べる濃度差が大きい。すなわち、ドライダウンが大きい(上図参照)。
ドライダウンに対する用紙の明確な要因がつかめていないため、用紙での対処法は非常に難しいのが現状である。例えば、比較的、ドライダウンの大きいマットコート紙で対策を取ろうとすれば、その最大の特徴である艶消しでしっとりした風合が失われるため実質の対応ができない。そのため印刷会社ではドライダウンを見込んでインキ量を増し(5~10%増)印刷、対処することが多い。すなわちドライダウンの程度はインキ、紙の種類(グレード)・銘柄などによって差があるので、トラブルを無くすか軽減するためには、そのインキで本紙校正し、ドライダウン特性を確認の上、インキ盛り量など最適印刷条件を設定することが重要で、最良である。なお、あらかじめ印刷用紙別のドライダウン特性データを作成しておき活用することもよい方法である。
スラー(スラーリング)
スラーは紙とブランケットとの間でスリップ現象が起こり、くわえ尻方向にぶれて網点・画線が2重になったり流れたりして、印刷が不鮮明になる現象をいう。すでに「紙の基礎講座 印刷編(1) 見当不良・印刷しわ・カール」の項で説明しているので省略する。
裏抜け・透き通し
用紙がらみの印刷物裏面汚れトラブルとして、既に説明したインキの乾燥に関係する裏移りと裏抜け、透き通しがある。ここでは裏抜け、透き通しについて概記する。
①裏抜け
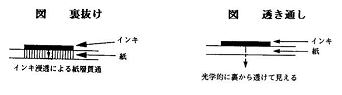
表面に印刷したインキ中の成分の一種(油分)が浸透し、部分的に裏面までしみ出して抜ける現象で、しみ通し、ストライクスルー(strike through)ともいう。すなわち印刷されたインキが透過し、裏面から見て透き通って見える状態をいう(右図参照)。比重の重い溶剤や植物油の多いインキと浸透の大きい紙の組合わせによって起こる浸透乾燥型インキの特徴で、紙が薄いと透き通しも並行して現れる。
②透き通し
表面の文字・絵柄が裏面(反対面)から透けて見える現象で、ショースルー(show through)ともいう(右図参照)。不透明度が低い用紙に濃厚なベタ刷りをした場合に発生しやすい現象で、対策としては、基本的に用紙は不透明性が高くて平滑度の高いものを選び、濃度のある高顔料インキを薄盛りしてあまり圧をかけないで印刷することである。
なお、同様な定義でプリントスルー(print through)という用語が使用されることがあるが、裏抜けと透き通しは同時に起こることがあるため明確な区別が難しく、また、原因と対策が類似していることから両者を合わせて、総称でプリントスルーと呼ばれることが多い。
印刷光沢不良
印刷光沢不良は一般的には、期待していたより印刷光沢が低い現象をいう。逆に印刷光沢を上げ過ぎるとインキ吸収性を抑えることとなり裏移り、ブロッキングや水負けによるインキ転移不良トラブルが発生しやすくなるので要注意である。なお、マット・ダル系の塗工紙で、印刷光沢が要求以上に高くなる場合も苦情となることがある。
ところで用紙サイドから見た場合、一般に白紙光沢と印刷光沢とは、相関関係があるので、いったん塗料組成・塗工量などが決まれば、印刷光沢の管理は、白紙光沢で管理をしているのが普通である。
耐光性不良(耐候性不良)…変色、退色、黄変、やけ
耐光性不良は太陽光(極端な場合は蛍光灯でも)によって、印刷物が変色したり、退色を起こしたりする現象をいう。他にも熱(温度)、湿度、染料などの化学物質、空気酸化などにより変・退色を起こすことがあり、用紙のみならず、インキ、フィルムなどの素材も変退色の対象になるので、それぞれの影響度を確認しておく必要がある。その上で個々について対策を講ずることが重要となる。
(2009年7月1日)
参考・引用資料
- 中嶋隆吉“紙 一紙と印刷、品質クレームへの対応一(下巻 増補改訂版)"(1997年12月)、王子製紙株式会社発行